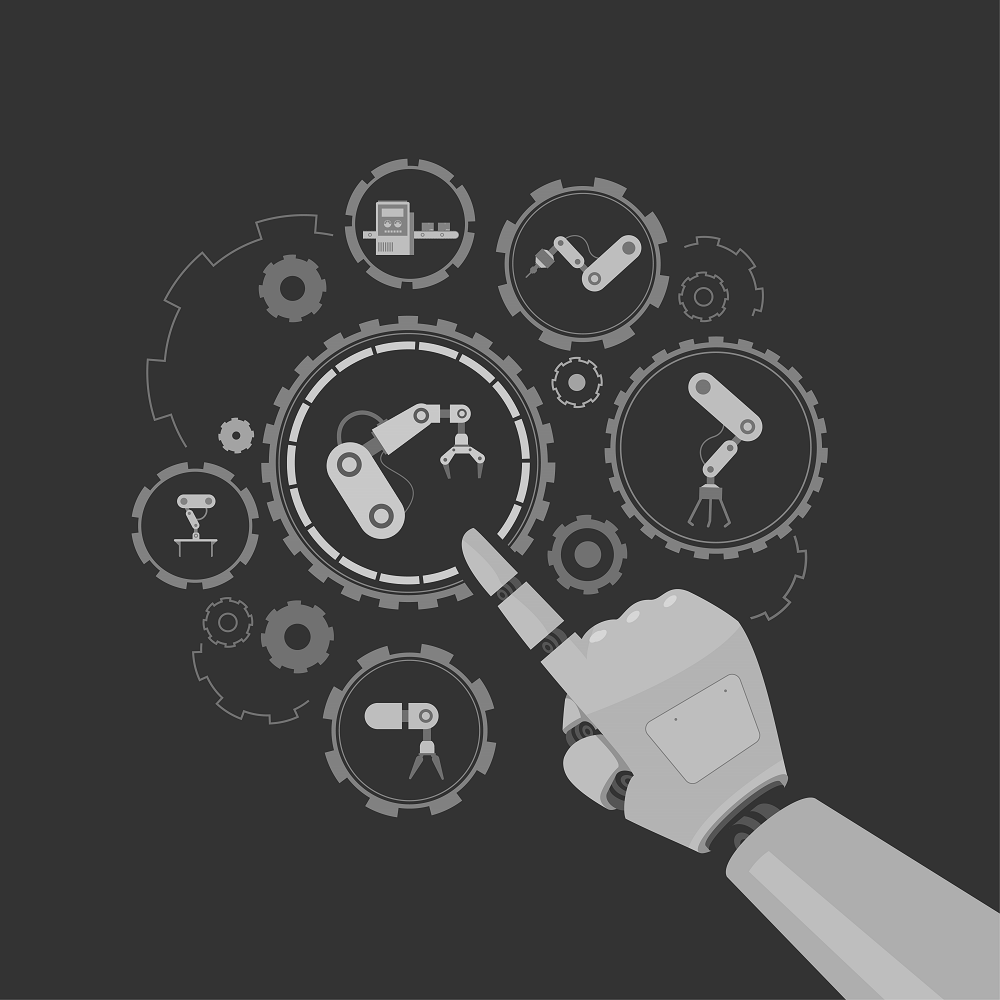
Understanding Thermal Heat Transfer in Machines: Processes and Types
Thermal heat transfer is a fundamental concept in the field of mechanical engineering, which involves the transfer of heat energy from one body to another. In machines, thermal heat transfer plays a critical role in maintaining proper operation and preventing overheating. This article aims to provide an in-depth understanding of thermal heat transfer in machines, including the types of heat transfer mechanisms, the processes involved, and the factors that affect transfer efficiency.
What is Thermal Heat Transfer in Machines?
Thermal heat transfer in machines is the process by which heat energy is transferred from a heat source to a heat sink. The heat source is the body or component that generates heat, such as a motor or a processor, while the heat sink is the component or medium that absorbs and dissipates heat, such as a heat sink or coolant.
Types of Thermal Heat Transfer in Machines
There are three types of thermal heat transfer mechanisms in machines: conduction, convection, and radiation.
1. Conduction Heat Transfer: This mechanism occurs when two objects at different temperatures come in direct contact with each other, allowing the heat energy to transfer from the hotter object to the cooler object. The rate of heat transfer by conduction is proportional to the temperature difference between the two objects and the thermal conductivity of the materials.
2. Convection Heat Transfer: This mechanism occurs when heat is transferred from a solid surface to a fluid, such as air or liquid, by the motion of the fluid. Convection heat transfer can be either natural or forced, depending on whether the motion of the fluid is due to natural buoyancy forces or external sources, such as fans or pumps.
3. Radiation Heat Transfer: This mechanism occurs when heat is transferred between two objects through electromagnetic waves. Radiation heat transfer does not require any physical contact between the two objects and can occur through a vacuum.
Processes Involved in Thermal Heat Transfer in Machines
The processes involved in thermal heat transfer in machines include the heat source, heat sink, thermal resistance, and thermal conductivity.
1. Heat Source: The heat source is the component or system that generates heat, such as a motor or an electronic circuit. The rate at which heat is generated depends on the power input and the efficiency of the system.
2. Heat Sink: The heat sink is the component or medium that absorbs and dissipates heat, such as a heat sink or coolant. The rate at which heat is dissipated depends on the surface area, the thermal conductivity of the material, and the temperature difference between the heat source and the heat sink.
3. Thermal Resistance: Thermal resistance is the measure of the resistance of a material to the flow of heat. The higher the thermal resistance, the lower the rate of heat transfer.
4. Thermal Conductivity: Thermal conductivity is the measure of the ability of a material to conduct heat. The higher the thermal conductivity, the higher the rate of heat transfer.
Factors Affecting Thermal Heat Transfer in Machines
Several factors affect the efficiency of thermal heat transfer in machines, including material properties, surface area, and temperature difference.
1. Material Properties: The thermal conductivity and specific heat capacity of the materials used in the machine components affect the rate of heat transfer. Materials with high thermal conductivity and low specific heat capacity are more effective in dissipating heat.
2. Surface Area: The surface area of the heat sink or the component in contact with the fluid affects the rate of heat transfer. Increasing the surface area increases the rate of heat transfer.
3. Temperature Difference: The temperature difference between the heat source and the heat sink affects the rate of heat transfer. A higher temperature difference results in a higher rate of heat transfer.
Importance of Thermal Management in Machines
Proper thermal management is critical in maintaining machine efficiency and preventing premature failure. Overheating can cause serious damage to the internal components of machines, leading to decreased performance and even complete system failure. In extreme cases, overheating can cause irreversible damage, rendering the machine unusable and requiring costly repairs or replacements.
To prevent overheating and ensure optimal performance, it is essential to understand the different types of thermal heat transfer mechanisms involved in machines. These mechanisms are conduction, convection, and radiation, and each plays a critical role in maintaining machine temperature within a safe range.
Conduction is the transfer of heat through a solid material, typically occurring in machine components such as heat sinks and heat pipes. This process relies on the material's ability to conduct heat, known as thermal conductivity, and the surface area available for heat transfer. A higher thermal conductivity and a larger surface area will result in more efficient heat transfer, ultimately reducing the risk of overheating.
Convection is the transfer of heat through a fluid, such as air or water, and occurs in systems such as cooling fans or liquid cooling systems. This process relies on the fluid's ability to absorb and transport heat away from the machine, as well as the design of the cooling system. Proper design and placement of cooling systems can significantly improve machine efficiency and reduce the risk of overheating.
Radiation is the transfer of heat through electromagnetic waves and occurs in systems such as infrared heaters or solar panels. This process relies on the material's ability to absorb and emit radiation, known as emissivity, and the temperature difference between the heat source and the heat sink. A higher emissivity and a larger temperature difference will result in more efficient heat transfer, ultimately reducing the risk of overheating.
In addition to understanding the different types of heat transfer mechanisms, it is essential to consider the factors that can affect thermal heat transfer in machines. Material properties, surface area, and temperature difference are the three primary factors that impact thermal conductivity and efficiency.
Material properties refer to the physical characteristics of the materials used in machine components, such as thermal conductivity, density, and specific heat. These properties can significantly impact heat transfer efficiency and must be carefully considered during the design and construction of machines.
Surface area refers to the total area available for heat transfer, and a larger surface area will result in more efficient heat transfer. Designing machines with optimal surface area can significantly improve thermal management and reduce the risk of overheating.
Temperature difference refers to the difference between the heat source and the heat sink and plays a critical role in determining the rate of heat transfer. A higher temperature difference will result in more efficient heat transfer, but it also increases the risk of overheating.
Proper thermal management is critical in maintaining machine efficiency and preventing premature failure. Overheating can cause serious damage to the internal components of machines, leading to decreased performance and even complete system failure. In extreme cases, overheating can cause irreversible damage, rendering the machine unusable and requiring costly repairs or replacements.
In addition to the negative impact on machine performance and longevity, overheating can also significantly increase energy consumption and costs. According to a study by the US Department of Energy, up to 50% of energy consumption in industrial facilities is due to the operation of machines and equipment. Proper thermal management can help reduce energy consumption and increase machine efficiency, ultimately saving companies money in the long run.
Examples of thermal heat transfer in machines can be found in a variety of practical applications. For example, cooling systems in cars use a combination of convection and radiation to transfer heat away from the engine and maintain optimal operating temperature. Heat sinks in computers use a combination of conduction and convection to transfer heat away from the CPU and other internal components. These examples highlight the importance of proper thermal management in ensuring machine efficiency and longevity.
Conclusion
In conclusion, thermal heat transfer is a critical component of machine design and operation. Understanding the different types of heat transfer mechanisms
and the processes involved in heat transfer is important for engineers and mechanics who are responsible for designing and maintaining machines. By carefully managing thermal heat transfer, it is possible to improve machine efficiency, increase lifespan, and reduce the risk of catastrophic failure.
It is essential to note that thermal heat transfer is not just an issue in industrial settings. In our daily lives, we encounter examples of thermal heat transfer all the time. For example, when we cook food on a stove or in an oven, heat is transferred from the heating element to the pot or pan, and then to the food. When we cool a room with an air conditioning unit, heat is transferred from the warm air in the room to the refrigerant in the unit, which then releases the heat outside.
Mechanical Engineering