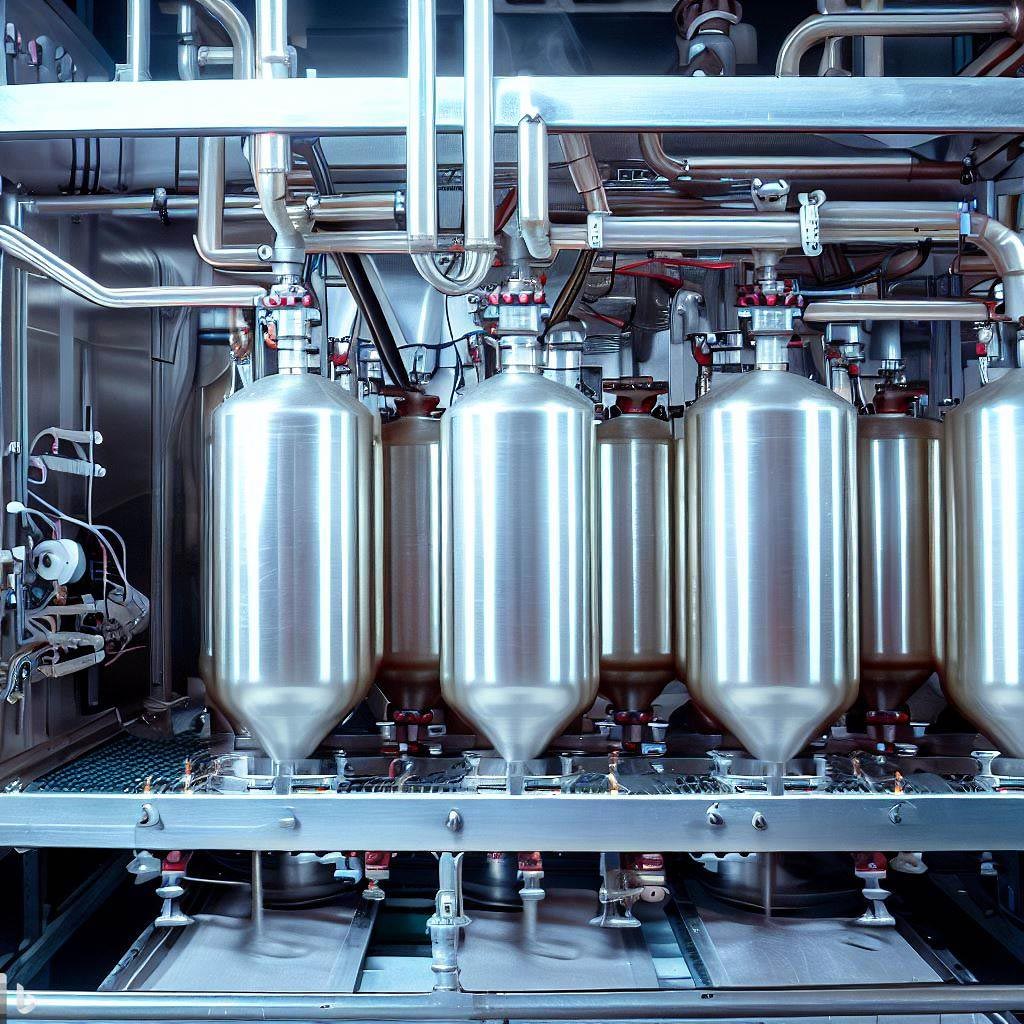
Ultrasonic Tubular Reactor: A Novel Technology for Producing High-Quality Pickering Emulsions
Ultrasonic technology has gained popularity in various industries due to its ability to enhance efficiency, reduce energy consumption, and produce high-quality products. One of the emerging ultrasonic technologies is the ultrasonic tubular reactor, which is used for emulsification processes. This article aims to explore the ultrasonic tubular reactor and its advantages over conventional ultrasound horn systems in producing high-quality Pickering emulsions.
Introduction
Ultrasonic tubular reactor is a novel technology that can be used to produce high-quality Pickering emulsions. The ultrasonic tubular reactor works by utilizing high-frequency sound waves to create cavitation in a liquid medium, which leads to the formation of microbubbles. The microbubbles then collapse and generate localized high temperatures and pressures, which can induce chemical reactions and physical changes in the liquid medium. The resulting cavitation activity and sonochemiluminescence can lead to the formation of stable Pickering emulsions.
Compared to conventional emulsification methods, such as mechanical stirring and homogenization, ultrasonic tubular reactor offers several advantages. Firstly, ultrasonic tubular reactor can produce emulsions with smaller and more uniform droplet size distribution, which leads to higher stability and improved functionality. Secondly, ultrasonic tubular reactor can reduce the processing time and energy consumption, which can lead to cost savings and improved efficiency. Thirdly, ultrasonic tubular reactor can operate at low temperatures and pressures, which can minimize the thermal and mechanical degradation of sensitive ingredients, such as proteins and enzymes.
In terms of performance, efficiency, and advantages, ultrasonic tubular reactor can also be compared with conventional ultrasound horn system. Ultrasonic tubular reactor offers higher productivity and scalability, since it can process large volumes of liquid continuously, whereas ultrasound horn system is limited by the batch size and processing time.
Pickering Emulsion
A Pickering emulsion is a type of emulsion stabilized by solid particles instead of surfactants. In conventional emulsions, surfactants are used to stabilize the interface between two immiscible liquids, such as oil and water. However, in Pickering emulsions, solid particles such as colloidal particles, nanoparticles, or micro-particles, are used instead of surfactants to stabilize the interface.
Pickering emulsions have several advantages over conventional emulsions. First, they offer improved stability and resistance to coalescence, which is the process by which droplets of one liquid merge together to form larger droplets. The solid particles at the interface prevent the droplets from coalescing, leading to more stable emulsions. Second, Pickering emulsions are often more resistant to changes in temperature, pH, and salt concentration, making them more suitable for a wide range of applications. Finally, Pickering emulsions can be easily produced using simple mixing techniques without requiring any additional energy input, making them a more cost-effective and environmentally friendly option.
Pickering emulsions have numerous potential applications in various fields, such as food, cosmetics, pharmaceuticals, and materials science. For example, in the food industry, Pickering emulsions can be used to produce stable emulsions for food products such as mayonnaise, salad dressings, and cream fillings. In the cosmetics industry, Pickering emulsions can be used to produce emulsions with improved texture and stability for creams, lotions, and sunscreens. In the pharmaceutical industry, Pickering emulsions can be used as drug delivery systems, providing improved stability and controlled release of drugs.
Cavitation Activity and Sonochemiluminescence
Ultrasonic tubular reactors generate high-frequency sound waves that propagate through the liquid medium, creating a series of alternating high- and low-pressure regions. In regions of low pressure, small gas bubbles are formed through the process of nucleation. These gas bubbles grow due to the reduction in pressure, and when they reach a critical size, they collapse violently, producing intense local heating and pressure waves. This process is called cavitation, and it generates a high amount of energy in the form of heat, light, and shockwaves.
The energy generated by cavitation can enhance the sonochemical reactions in the liquid medium, leading to the production of reactive radicals and species, such as hydrogen peroxide, hydroxyl radicals, and ozone. These reactive species can promote chemical reactions and physical processes, such as emulsification, dispersion, and dissolution, which can improve the emulsion quality and stability.
Moreover, the collapse of cavitation bubbles can also generate light, a phenomenon called sonochemiluminescence. The intensity of the light emission is proportional to the cavitation activity, and it can be used as an indicator of the sonochemical activity in the liquid medium. By monitoring the sonochemiluminescence, it is possible to optimize the ultrasonic parameters, such as frequency, power, and treatment time, to maximize the cavitation activity and improve the emulsion quality and stability.
Therefore, by enhancing the cavitation activity and sonochemiluminescence, ultrasonic tubular reactors can improve the emulsion quality and stability by promoting the formation of smaller droplets with a more homogeneous distribution, reducing the size and number of the larger droplets, and preventing coalescence and Ostwald ripening. Additionally, the sonochemical reactions can also improve the shelf life, sensory properties, and functional properties of the emulsions by reducing the microbial growth, oxidative degradation, and other degradation reactions.
Energy Consumption and Environmental
Impact Ultrasonic tubular reactor can reduce the energy consumption and environmental impact of emulsification by using less power, less surfactant, and less waste generation. The high-intensity ultrasound waves generated by the transducer can break down the oil and water droplets into smaller sizes, which require less energy to be emulsified. The solid particles used in Pickering emulsions also reduce the need for surfactants, which can have negative effects on the environment. Moreover, the ultrasonic tubular reactor produces less waste than conventional emulsification methods, as it does not require the use of hazardous chemicals or complex equipment.
Applications
Ultrasonic tubular reactor can be applied in various industries such as food, cosmetics, pharmaceuticals, and others to produce high-quality and stable emulsions with desired properties and functions. For example, in the food industry, ultrasonic tubular reactor can be used to produce mayonnaise, sauces, dressings, and other emulsified products with a smooth texture, high stability, and improved sensory properties. In the cosmetics industry, ultrasonic tubular reactor can be used to produce creams, lotions, and other emulsions with a fine and homogeneous distribution of particles, which can improve the skin penetration and efficacy of the products. In the pharmaceutical industry, ultrasonic tubular reactor can be used to produce drug delivery systems, vaccines, and other products that require stable and homogeneous emulsions.
The advantages of using an ultrasonic tubular reactor in these industries include reduced processing time, improved efficiency, and increased product quality. Ultrasonic waves can break down large droplets into smaller ones, which leads to a higher surface area and better emulsification. This results in emulsions that are more stable, have a longer shelf life, and exhibit improved functional properties.
Moreover, ultrasonic tubular reactors are also environmentally friendly and energy-efficient. They do not require any solvents or chemicals, which reduces the use of hazardous substances and minimizes waste. Additionally, ultrasonic waves require less energy to produce emulsions compared to traditional mechanical methods.
Comparison: Explain how ultrasonic tubular reactor can be compared with conventional ultrasound horn system in terms of performance, efficiency, and advantages
Ultrasonic tubular reactors and conventional ultrasound horn systems are two types of ultrasonic devices that are commonly used for various industrial applications. Here are some comparisons between the two:
Performance: Ultrasonic tubular reactors typically have better performance than conventional ultrasound horn systems. This is because ultrasonic tubular reactors provide a more uniform distribution of cavitation bubbles and acoustic energy throughout the liquid medium. This results in more efficient emulsification, dispersion, and mixing. In contrast, conventional ultrasound horn systems tend to create hot spots and cold spots in the liquid medium, which can result in uneven processing and lower efficiency.
Efficiency: Ultrasonic tubular reactors are generally more efficient than conventional ultrasound horn systems. This is because ultrasonic tubular reactors use less power and require less maintenance compared to ultrasound horn systems. Ultrasonic tubular reactors also have higher processing capacity and throughput, which can result in significant cost savings and improved productivity.
Advantages: Ultrasonic tubular reactors offer several advantages over conventional ultrasound horn systems. They have a more compact design and can be easily integrated into existing production lines. Ultrasonic tubular reactors also have a longer service life and require less maintenance compared to ultrasound horn systems. In addition, ultrasonic tubular reactors can be used for a wide range of applications, including food processing, chemical synthesis, and pharmaceutical manufacturing.
Overall, ultrasonic tubular reactors are a more advanced and efficient ultrasonic device compared to conventional ultrasound horn systems. They offer better performance, higher efficiency, and several advantages that make them a preferred choice for many industrial applications.
Conclusion
In summary, ultrasonic tubular reactors are a promising technology for producing high-quality and stable emulsions with desirable properties and functions in various industries. With their advantages over traditional methods, ultrasonic tubular reactors have the potential to revolutionize the way emulsions are produced and pave the way for more sustainable and efficient production processes.
Engineering Topics