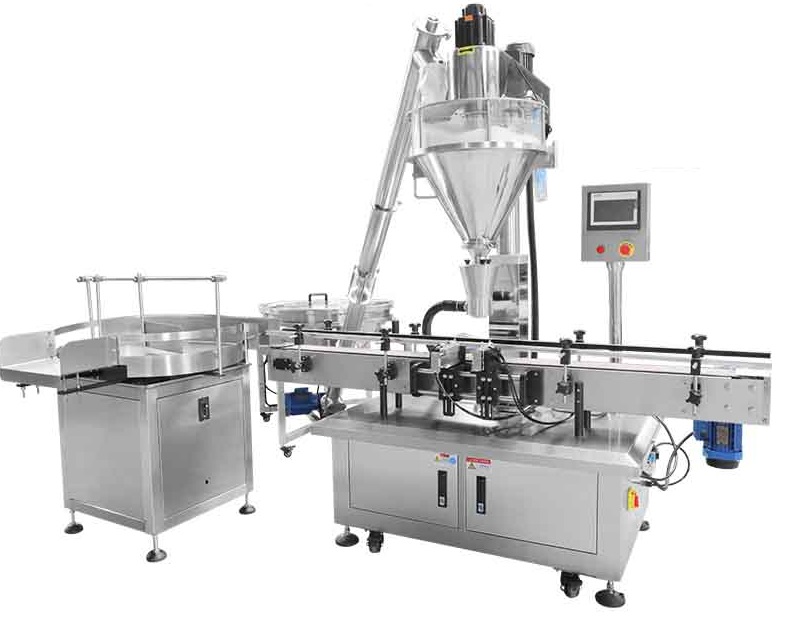
The Future of Filling Machine Technology: Emerging Trends and Innovations
The world of manufacturing is undergoing a constant evolution, driven by relentless innovation and technological advancements. Filling machines, a cornerstone of countless industries, are no exception. As consumer demands shift and technological boundaries are pushed, filling machine technology is poised for a future brimming with exciting trends and improvements. This article delves into these emerging trends, exploring how they will revolutionize the way products are filled and packaged.
1. The Rise of Smart Filling Machines: Industry 4.0 Integration
One of the most significant trends shaping the future of filling machines is the integration of Industry 4.0 principles. This refers to the increasing automation, data exchange, and interconnection of machines within a manufacturing environment. Filling machines are becoming "smart" by incorporating features like:
- Industrial Internet of Things (IIoT): Sensors embedded within the machine collect real-time data on operational parameters like filling speed, product consistency, and energy consumption. This information can be transmitted to a central control system for analysis and optimization. Learn more about Filling Machines
- Machine Learning and Artificial Intelligence (AI): By analyzing historical data and real-time sensor readings, AI algorithms can learn to predict potential issues and optimize filling processes for maximum efficiency and accuracy.
- Predictive Maintenance: AI can analyze data patterns to anticipate maintenance needs before equipment failures occur, minimizing downtime and production disruptions.
The benefits of smart filling machines are numerous. They enable:
- Increased Efficiency: Optimizing filling processes through data analysis leads to faster filling times and reduced product waste.
- Enhanced Accuracy: AI-powered systems can ensure consistent fill levels and product quality, minimizing deviations from specifications.
- Improved Productivity: Predictive maintenance and real-time monitoring minimize downtime and ensure smooth operation.
- Reduced Costs: Optimized processes and predictive maintenance lead to lower operational costs and higher profitability.
2. Versatility and Adaptability: Filling Machines for Diverse Applications
The filling machine landscape is shifting towards greater versatility and adaptability. Manufacturers are developing machines that can handle a wider range of products and packaging formats. This includes:
- Multi-head Filling Systems: These machines use multiple filling heads for simultaneous filling of multiple containers, significantly increasing production speed.
- Configurable Filling Lines: Modular components allow for easily customizing filling lines to accommodate different products and packaging needs.
- Aseptic Filling Systems: For products requiring sterile environments, advancements in aseptic filling technology ensure product integrity and safety.
This increased versatility empowers manufacturers to:
- Expand Product Lines: Easily adapt filling processes to accommodate new product introductions.
- Reduce Capital Expenditures: A single adaptable machine can handle various products, eliminating the need for dedicated equipment.
- Respond to Market Trends: Quickly adapt production lines to cater to changing consumer preferences and packaging formats.
3. Sustainable Practices: Eco-Conscious Filling Machines
Sustainability is a growing concern across industries, and filling machine manufacturers are taking note. This translates into several key trends:
- Energy-Efficient Design: Machines are being designed with energy-efficient motors and components, reducing their environmental footprint.
- Recyclable Materials: The use of recyclable materials in machine construction minimizes waste and promotes environmental responsibility.
- Reduced Waste Generation: Advancements in filling technology lead to less product waste during the filling process.
These sustainable practices benefit manufacturers by:
- Lowering Energy Consumption: Reduced energy usage translates to lower operational costs and a smaller carbon footprint.
- Improving Brand Image: Consumers are increasingly drawn to brands committed to sustainability.
- Compliance with Regulations: Filling machines may need to comply with stricter environmental regulations in the future.
4. Enhanced User Experience: User-Friendly and Intuitive Controls
In today's fast-paced world, user experience is paramount. Filling machine manufacturers are prioritizing user-friendliness through:
- Intuitive Touchscreen Interfaces: Replacing complex control panels with intuitive touchscreens simplifies operator interaction and reduces training time.
- Remote Monitoring and Control: Operators can monitor and control filling processes remotely via smartphones or tablets, enabling greater flexibility and convenience.
- Modular Design: This simplifies maintenance and cleaning, reducing downtime and overall operating costs.
An enhanced user experience leads to:
- Reduced Training Time: Easy-to-use systems minimize training requirements and ensure faster operator proficiency.
- Improved Operator Efficiency: Intuitive controls allow operators to focus on production rather than struggling with complex interface navigation.
- Increased Operator Satisfaction: A user-friendly experience fosters operator satisfaction and promotes a positive work environment.
5. Cybersecurity: Ensuring Data Protection and Operational Integrity
As filling machines become increasingly connected and data-driven, cybersecurity becomes a critical concern. Manufacturers are implementing measures to protect their machines and networks from cyber threats, including:
- Robust Network Security: Implementing firewalls, intrusion detection systems, and regular security audits to safeguard against unauthorized access.
- Secure Data Transmission: Encrypting data to protect sensitive information during transmission.
- Regular Software Updates: Keeping machine software up-to-date to address vulnerabilities and security patches.
Strong cybersecurity practices are essential to:
- Protect Sensitive Data: Prevent unauthorized access to proprietary information and customer data.
- Maintain Operational Continuity: Minimize the risk of disruptions caused by cyberattacks.
- Comply with Regulations: Adhere to industry-specific data protection standards.
Conclusion
The future of filling machine technology is marked by exciting advancements that will reshape the manufacturing landscape. From smart machines to sustainable practices and enhanced user experiences, these trends are driving the industry towards greater efficiency, productivity, and sustainability. By embracing these innovations, manufacturers can position themselves for success in a rapidly evolving market and meet the ever-changing demands of consumers.