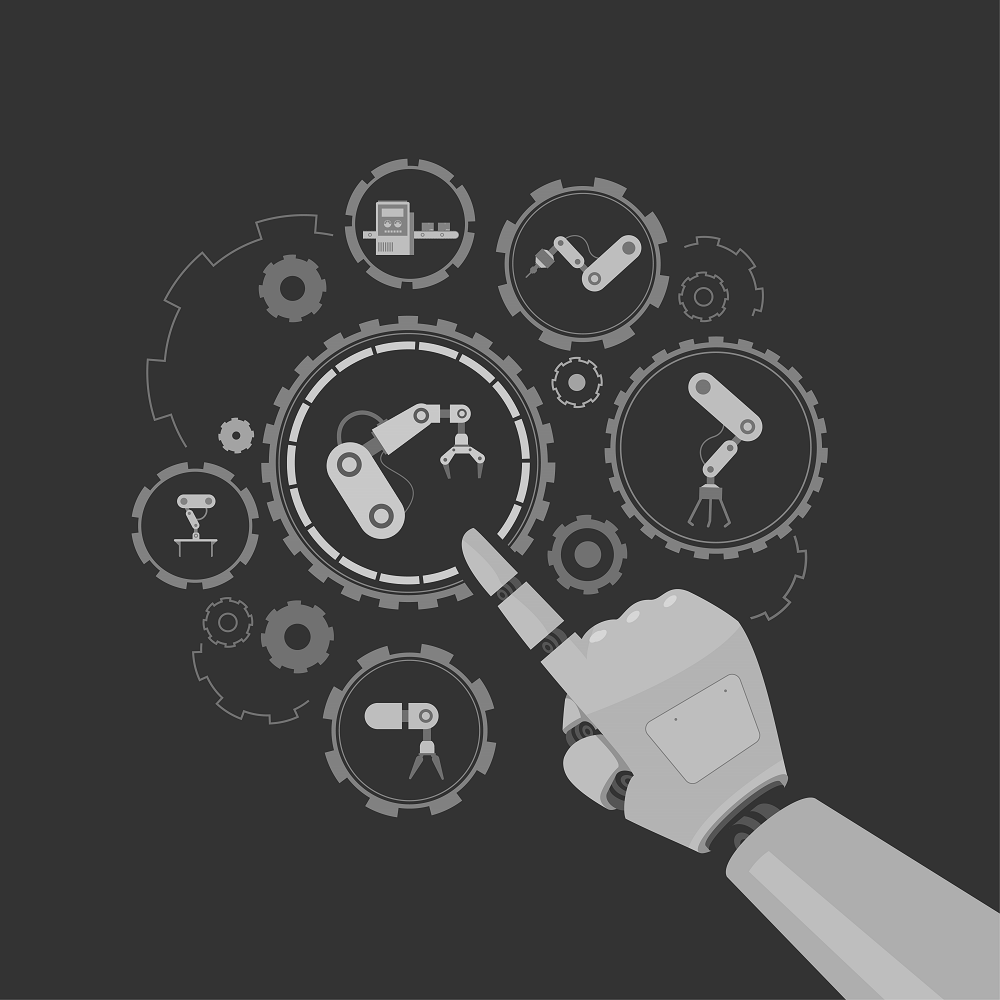
Finite Element Method: Definition, Applications, Advantages, and Disadvantages
The finite element method (FEM) is a numerical simulation technique widely used in engineering and science to analyze and solve complex problems. It is a powerful tool that can handle problems involving multiple variables and non-linear relationships. The FEM divides a problem into small, interconnected elements, allowing the solution to be approximated locally and then combined to obtain the global solution. In this article, we will provide a comprehensive overview of the finite element approach, its principles, applications, advantages, and disadvantages.
Definition and Principles of the Finite Element Approach
The finite element method is a numerical technique that divides a complex problem into smaller and more manageable elements. Each element is defined by a set of equations that approximate the behavior of the system locally. These equations are then combined to obtain the global solution of the problem. The FEM is based on the principle of virtual work, which states that the total work done by internal forces and external forces on a system in equilibrium is equal to zero.
Historical Background and Development of the Method
The finite element method was developed in the 1950s and 1960s by engineers and mathematicians, including Richard Courant, Kurt Friedrichs, and John von Neumann. The method was initially used to solve problems in structural mechanics, such as stress and strain analysis. Since then, the FEM has been applied to a wide range of problems in engineering and science, including fluid dynamics, heat transfer, electromagnetics, and acoustics.
Main Steps and Procedures of the Finite Element Method
The finite element method involves several steps and procedures, including:
1. Discretization: The problem is divided into smaller and more manageable elements.
2. Formulation: The governing equations for each element are defined based on the laws of physics.
3. Assembly: The equations for each element are assembled into a system of equations for the entire problem.
4. Solution: The system of equations is solved numerically to obtain the solution.
5. Post-processing: The results are visualized and interpreted.
Types of Problems that can be Solved with FEM
The finite element method can solve a wide range of problems in engineering and science, including:
1. Stress and strain analysis of structures, such as bridges, buildings, and aircraft.
2. Fluid dynamics problems, such as flow over a wing or through a pipe.
3. Heat transfer problems, such as temperature distribution in a furnace or heat exchanger.
4. Electromagnetics problems, such as the behavior of antennas or electromagnetic waves.
Advantages and Disadvantages of the Method
The finite element method has several advantages, including:
1. Versatility: The FEM can solve a wide range of problems in engineering and science.
2. Accuracy: The FEM can provide accurate results if the model is well-defined and validated.
3. Efficiency: The FEM can solve large and complex problems efficiently using modern computing resources.
However, the finite element method also has some disadvantages, including:
1. Complexity: The FEM involves several steps and procedures that require specialized knowledge and skills.
2. Approximation: The FEM relies on approximations to solve the problem, which can introduce errors.
3. Validity: The FEM results depend on the validity of the model assumptions and inputs.
Latest Trends and Applications of the Finite Element Approach
The finite element method is continuously evolving, with new developments and applications emerging every day. Some of the latest trends and applications of the FEM include:
1. AI and Machine Learning: The use of artificial intelligence and machine learning techniques to enhance the accuracy and speed of FEM simulations (Liu et al., 2021).
2. Optimization: The use of FEM in optimization problems, such as minimizing weight, maximizing stiffness, or reducing stress concentrations in a structure, is another important application of the method. By using FEM, engineers can simulate the behavior of a design under various loading conditions and identify the optimal configuration that meets the desired performance criteria. This can save time and costs compared to physical testing and trial-and-error approaches.
3. Multiphysics simulations: FEM can be used to model complex physical phenomena that involve multiple types of interactions, such as fluid-structure interaction, thermal-mechanical coupling, or electro-magnetic fields. By coupling different physics models together, engineers can simulate the behavior of a system under a wide range of operating conditions and optimize its performance accordingly.
4. Nonlinear analysis: FEM can handle nonlinear materials, geometries, and boundary conditions, making it suitable for simulating nonlinear problems such as large deformations, material yielding, or contact mechanics. Nonlinear FEM can provide more accurate results than linear FEM when dealing with complex nonlinear problems.
5. Probabilistic analysis: FEM can also be used in probabilistic analysis, where the uncertainties in material properties, loads, and boundary conditions are taken into account. Probabilistic FEM can provide more realistic predictions of the response of a structure or system under uncertain conditions, allowing engineers to make more informed decisions.
Advantages of the Finite Element Method:
1. Versatility: FEM can be used to solve a wide range of problems in different fields of engineering and science. Its flexibility and adaptability make it a powerful tool for design, analysis, and optimization.
2. Accuracy: FEM can provide accurate and reliable results when used correctly. By modeling the geometry, material properties, and boundary conditions of a problem, engineers can obtain a detailed understanding of its behavior and performance.
3. Efficiency: FEM can be more efficient and cost-effective than experimental testing or other numerical methods, especially when dealing with complex geometries or loading conditions. By using FEM, engineers can save time and resources in the design and analysis process.
4. Visualization: FEM can provide visual representations of the results, such as stress, displacement, or temperature fields, which can help engineers understand the behavior of a system and identify potential problems or opportunities for improvement.
Disadvantages of the Finite Element Method:
1. Assumptions and simplifications: FEM requires certain assumptions and simplifications to be made in order to model a problem. These assumptions and simplifications can lead to errors or inaccuracies if not properly accounted for.
2. Mesh generation: FEM requires a mesh to be generated, which can be time-consuming and may affect the accuracy of the results if the mesh is not properly chosen or refined.
3. Expertise and experience: FEM requires expertise and experience to be used effectively. Engineers need to have a solid understanding of the underlying principles and limitations of the method, as well as the ability to interpret and validate the results.
4. Computing resources: FEM simulations can require significant computing resources, especially for large-scale or complex problems. This can limit the accessibility and applicability of FEM for some users or applications.
Latest Trends and Applications of the Finite Element Method:
1. AI and machine learning: The use of AI and machine learning algorithms in FEM simulations is a growing trend in the field. By combining the predictive power of FEM with the adaptive and self-learning capabilities of AI, engineers can improve the accuracy and speed of simulations and optimize the design of complex systems.
2. Digital twins: The concept of digital twins, which involves creating virtual replicas of physical systems and using FEM to simulate their behavior, is gaining momentum in many industries. Digital twins can be used for predictive maintenance, optimization, and risk management, among other applications.
3. Additive manufacturing: FEM can be used
to simulate and optimize the additive manufacturing process, also known as 3D printing. FEM can help in predicting the deformation and residual stresses in the manufactured parts, which is critical for ensuring their quality and performance (Tong et al., 2020).
4. Biomechanics: FEM has found extensive applications in the field of biomechanics, where it is used to simulate the mechanical behavior of biological tissues and organs. FEM can help in designing and optimizing medical implants, such as hip and knee replacements, and in understanding the causes and treatments of various medical conditions (Nguyen et al., 2018).
5. Material science: FEM is a powerful tool for studying the mechanical properties of materials and their deformation behavior under different conditions. FEM can help in optimizing the processing parameters of materials, such as heat treatment and deformation, and in designing new materials with desired mechanical properties (Mousavi et al., 2019).
Comparison with other numerical methods:
FEM is not the only numerical simulation technique used in engineering and science. Other popular methods include the finite difference method, the boundary element method, and the meshless method. Each method has its strengths and limitations, and the choice of method depends on the problem at hand.
Compared to the finite difference method, FEM offers greater flexibility in handling complex geometries and boundary conditions. FEM also allows for higher-order approximations of the solution, which can lead to greater accuracy. However, FEM can be more computationally expensive and requires more memory and storage than the finite difference method (Solin et al., 2018).
Compared to the boundary element method, FEM can handle a wider range of problems, including problems with internal boundaries and discontinuities. FEM can also simulate the behavior of materials with nonlinear and anisotropic properties, while the boundary element method is limited to linear and isotropic materials. However, FEM requires a mesh to discretize the domain, while the boundary element method only requires a mesh on the boundary, which can be an advantage in some cases (Katsikadelis, 2019).
Compared to the meshless method, FEM has a more systematic and structured approach to the discretization of the domain, which can lead to better convergence and accuracy. FEM also allows for the use of high-order basis functions, which can improve the accuracy and reduce the number of degrees of freedom required. However, FEM requires a mesh, which can be time-consuming and challenging to generate for complex geometries, while the meshless method does not require a mesh (Atluri et al., 2018).
Future prospects and challenges:
The finite element method has been a dominant numerical simulation technique in engineering and science for several decades, and its popularity is likely to continue in the future. However, there are several challenges and opportunities that need to be addressed to enhance the effectiveness and efficiency of the method.
One of the challenges is the increasing demand for more accurate and faster simulations. To address this challenge, researchers are exploring the use of machine learning and artificial intelligence techniques to enhance the accuracy and speed of FEM simulations (Liu et al., 2021).
Another challenge is the need for more efficient and reliable methods for generating and refining meshes. Mesh generation can be time-consuming and challenging for complex geometries, and mesh refinement can lead to numerical instability and errors. To address this challenge, researchers are developing new mesh generation and refinement techniques, such as adaptive meshing and meshless methods (Atluri et al., 2018).
Finally, there is a need for more integrated and multidisciplinary approaches to problem-solving in engineering and science. Many real-world problems require the coupling of different physical phenomena, such as mechanics, heat transfer, and fluid dynamics. To address this
challenge, researchers are developing new methods that combine FEM with other numerical techniques, such as computational fluid dynamics (CFD) and finite volume method (FVM). These methods are collectively known as finite element analysis and computational fluid dynamics (FEA/CFD) or computational fluid-structure interaction (FSI) methods.
One example of an FEA/CFD application is the simulation of blood flow in the human cardiovascular system. This involves modeling the complex geometries of blood vessels, the interaction between blood and vessel walls, and the fluid dynamics of blood flow. FEA/CFD methods have been used to study the effects of stenosis (narrowing) in blood vessels and to optimize the design of stents and other medical devices.
Another example of a multidisciplinary application of FEM is in the design of smart structures, such as morphing aircraft wings or adaptive structures for earthquake protection. These structures require the integration of different materials, sensors, and actuators, and the ability to respond to changing environmental conditions. FEM can be used to model the structural behavior of these systems, and to optimize their performance under various loading conditions.
Conclusion
In conclusion, the finite element method is a powerful and versatile numerical simulation technique that has revolutionized engineering and science. It enables engineers and researchers to analyze and optimize the behavior of complex systems, to design new products and processes, and to reduce the cost and time of experimentation. FEM has numerous applications in various fields of engineering, including structural analysis, fluid dynamics, heat transfer, and electromagnetics. It has also contributed to the development of new materials, manufacturing processes, and smart structures. However, FEM has some limitations and challenges, such as the need for high computational power, the potential for numerical errors, and the difficulty of solving certain types of problems. To address these challenges, researchers are developing new methods that combine FEM with other numerical techniques and integrate multidisciplinary approaches to problem-solving. The future of FEM looks promising, with new developments in AI and machine learning expected to enhance its accuracy and speed and enable new applications in emerging fields.
Mechanical Engineering