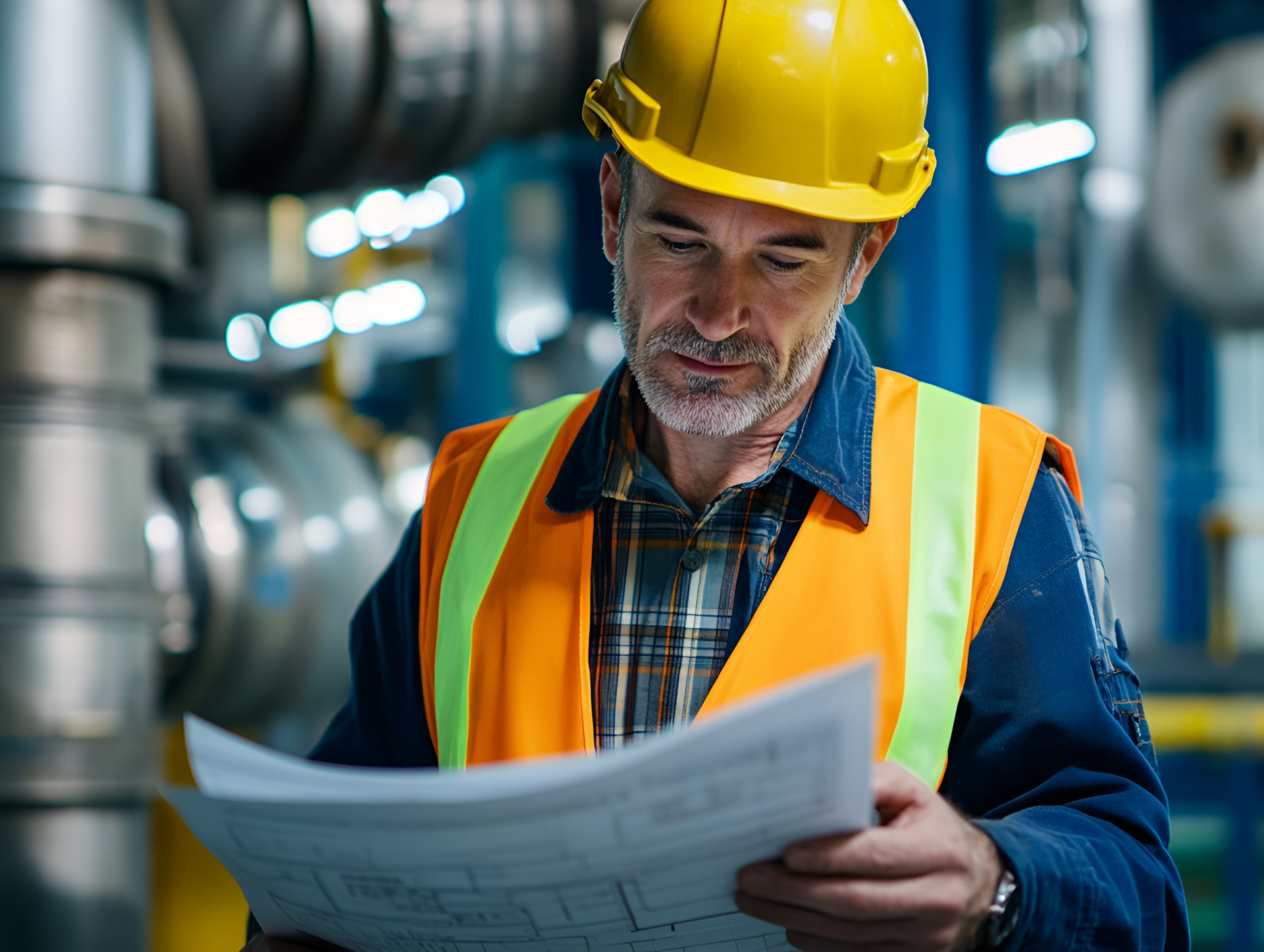
Engineering Economics: Cost Analysis and Financial Decision-Making in Projects
In today’s rapidly evolving world, engineering projects are becoming increasingly complex. With large budgets and high stakes, efficient cost analysis and effective financial decision-making are crucial for ensuring project success. The field of engineering economics provides the tools necessary to assess project costs, evaluate alternatives, and make sound financial decisions that maximize profitability and sustainability.
This article will explore the key principles of engineering economics, focusing on cost analysis techniques and financial decision-making frameworks that engineers and project managers can use to optimize project outcomes.
Introduction
Managing large-scale engineering projects is no easy feat. Whether you're designing infrastructure or implementing new technologies, it’s essential to keep financial constraints and cost analysis at the forefront of planning. The primary challenge for engineers is to balance cost efficiency with quality and innovation. This is where engineering economics steps in, offering the right blend of economic evaluation tools to make informed decisions. But how exactly can you make the best financial decisions for your project? And what methods can you apply for accurate cost estimation?
In this guide, we'll explore how to leverage cost analysis techniques and financial decision-making models to streamline project planning, minimize financial risk, and ensure long-term project success.
The Role of Engineering Economics in Projects
Engineering economics is the application of economic principles to engineering projects. It involves evaluating the costs, benefits, and economic viability of proposed projects, thereby guiding decision-making processes. At its core, engineering economics enables professionals to assess different investment opportunities, estimate financial returns, and make informed decisions about the allocation of resources.
Key Cost Analysis Techniques in Engineering
Cost analysis plays a central role in determining the viability of a project. Here are several cost analysis techniques commonly used in engineering:
1. Life Cycle Cost Analysis (LCCA)
LCCA is a method of calculating the total cost of ownership of an asset over its entire lifespan. It includes initial investment costs, operational costs, maintenance expenses, and disposal costs. This analysis helps engineers determine which project alternative offers the lowest overall cost and is most cost-effective in the long run.
Benefits of LCCA:
- Provides a comprehensive view of all costs.
- Helps in making decisions based on long-term benefits rather than short-term gains.
- Enhances sustainability by considering maintenance and disposal costs.
2. Cost-Benefit Analysis (CBA)
CBA involves comparing the benefits and costs of a project to determine its feasibility. By quantifying the benefits (in monetary terms) and subtracting the costs, engineers can assess whether a project is financially viable.
Advantages of CBA:
- Simplifies decision-making by quantifying benefits and costs.
- Helps prioritize projects with the highest return on investment (ROI).
- Increases transparency by clearly outlining economic gains.
3. Discounted Cash Flow (DCF)
The DCF method evaluates the present value of future cash flows generated by a project. It accounts for the time value of money (TVM), which assumes that a dollar today is worth more than a dollar in the future. DCF is particularly useful in assessing large, long-term engineering projects where future cash flows are uncertain.
DCF Key Metrics:
- Net Present Value (NPV): The difference between the present value of cash inflows and outflows. A positive NPV indicates a profitable project.
- Internal Rate of Return (IRR): The interest rate at which NPV equals zero. A higher IRR signifies a more attractive investment.
4. Break-even Analysis
Break-even analysis identifies the point at which total costs and total revenues are equal, meaning the project neither gains nor loses money. This technique is invaluable for determining the minimum performance a project must achieve to cover its costs.
Break-even Analysis Benefits:
- Determines the financial feasibility of a project.
- Helps engineers understand the impact of variable and fixed costs on profitability.
- Provides insight into the level of demand required to sustain the project.
Financial Decision-Making Models
In addition to cost analysis techniques, engineers rely on various financial decision-making models to guide project investments and evaluate the financial sustainability of different project options. Some of the most common models include:
1. Capital Budgeting
Capital budgeting refers to the process of evaluating and selecting long-term investment projects. Engineers use this method to determine whether a project’s future cash inflows justify the initial investment. Capital budgeting tools like NPV, IRR, and Payback Period allow engineers to assess project risks and returns.
Importance of Capital Budgeting:
- Ensures investments are financially viable.
- Helps in resource allocation by evaluating project profitability.
- Facilitates long-term planning and strategic growth.
2. Sensitivity and Scenario Analysis
Sensitivity analysis assesses how different variables (such as costs, revenues, or interest rates) affect project outcomes. Scenario analysis, on the other hand, evaluates how various potential future events (e.g., economic downturns or market changes) might impact the project’s financial success.
Benefits of These Methods:
- Allows engineers to understand the range of potential outcomes.
- Helps in identifying risks and mitigating them effectively.
- Increases confidence in financial decisions by modeling various scenarios.
3. Opportunity Cost
Opportunity cost measures the potential benefits an individual, investor, or business misses out on when choosing one alternative over another. In engineering projects, understanding the opportunity cost helps decision-makers evaluate trade-offs between competing project options.
Example:
If an engineering firm has a choice between investing in renewable energy technology or improving existing infrastructure, the opportunity cost is the potential profit lost from not choosing the most lucrative option.
Real-World Applications of Cost Analysis and Financial Decision-Making
The principles of cost analysis and financial decision-making are essential in various engineering sectors, including construction, manufacturing, and energy. Here are a few real-world applications:
-
Infrastructure Projects: Large-scale infrastructure projects, such as road and bridge construction, require careful cost analysis and financial planning. Engineers must evaluate different materials, construction methods, and timelines to minimize costs while maintaining quality.
-
Manufacturing Plants: In manufacturing, companies use capital budgeting techniques to decide on upgrading equipment or investing in new production lines. The use of life cycle cost analysis helps manufacturers estimate long-term costs and benefits.
-
Energy Sector: In the renewable energy sector, cost-benefit analysis is crucial in deciding whether to invest in solar or wind energy projects. Engineers must weigh the high initial capital costs against the long-term environmental and financial benefits.
Conclusion
Effective cost analysis and financial decision-making are critical components of successful engineering projects. By applying methods such as life cycle cost analysis, discounted cash flow, and capital budgeting, engineers can make informed financial decisions that lead to cost-efficient and profitable outcomes.
Whether you are managing a small project or a large-scale infrastructure development, incorporating the principles of engineering economics ensures that your financial decisions align with project goals, reduce risks, and maximize returns.
Engineering Topics